Dry drum permanent magnetic separator is a kind of magnetic separation equipment which can automatically and continuously remove iron from the dry powder material. It's mainly suitable for the arid regions or the materials can't allowed to touch water. It can be used for iron pollutants removing of fine powder or granular materials, such as purification of refractories, glass, ceramics, abrasives, quartz, feldspar and other non-metallic minerals, and dry primary separation of ilmenite, chromite, manganese ore, garnet, hematite and limonite or other minerals with difference of magnetic.
The core parts of the machine are made of high performance rare earth NdFeB, the surface magnetic intensity could be 1000-15000gs. The drum body is made of stainless steel which is non-magnetic and durable. It's equipped with stepless speed regulation motor, which can adjust 1-5 times of rotating speed by revolve the hand wheel at the upper end of motor. Usually, dry magnetic separator has a iron removing drum on the top, the raw ore can get iron removing treatment first before purification, less processing machine, makes the operation more simple.
Dry drum permanent magnetic separator working principle
The machine is mainly composed of hopper, electromagnetic speed regulation transmission, weak magnetic drum of iron removing, strong magnetic drum of weak magnetic minerals, splitter plate, magnetic concentrate discharge hole, middling discharge hole, tailing discharge hole and other parts. The material fed into the hopper, the ferromagnetic minerals (Fe3O4) in the mineral are firstly removed through the weak magnetic drum of iron removing, and then the material through the strong magnetic drum, the weak magnetic minerals affected by strong magnetism and the non-magnetic minerals affected by centrifugal force of rotation of drum, they fall off with different tracks and be separated by the splitter plate, so as to achieve the purpose of separation.
Advantages and features
1. The magnetic is high performance rare earth NdFeB, high magnetic field intensity and strong magnetic attraction;
2. Low power consumption and low ore operation cost;
3. Less wearing parts, no maintenance, reliable and safe;
4. Continuous automatic iron pollutants removing, easy operation;
5. Can be made into two or more drums;
6. There are various magnetic forces to choose from (1000-15000Gs).
(According to the material to determine the magnetic intensity of each magnetic roller) the following is for reference only:
The first stage magnetic separation: permanent magnetic drum 2000-5000gs
The second stage magnetic separation: magnetic roller 7000-9000gs
Third stage magnetic separation: magnetic roller 9000-15000gs
Main technical parameters
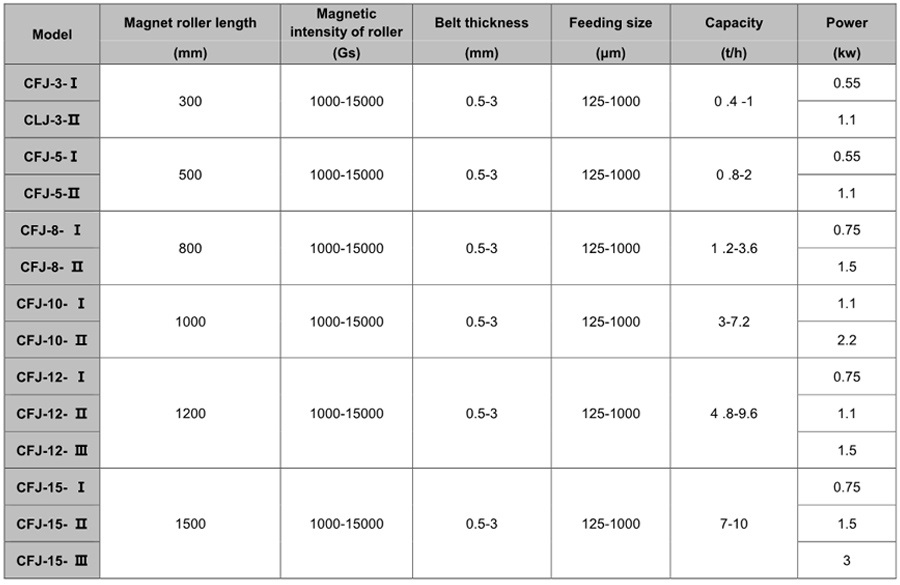